Guidelines
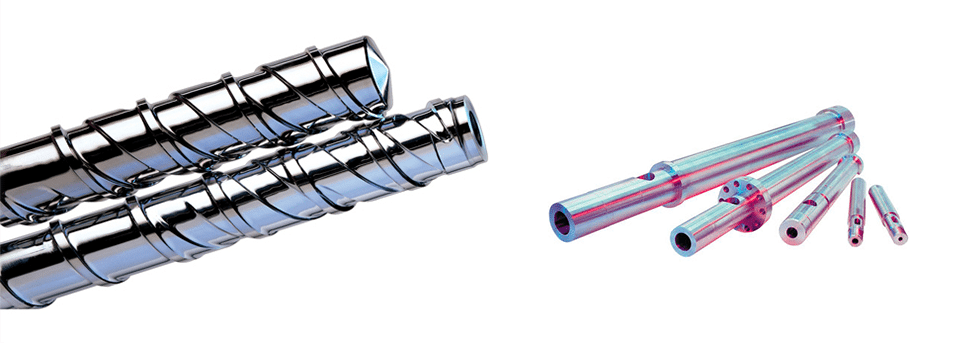
These are the Recommended Maximum Wear Clearances between screw and barrel for best output performance | |||
---|---|---|---|
Screw Size | New Part Clearance | Worn Clearance | Max Wear Clearance |
1″ | .003-.004″ | .018″ | .020″ |
1-1/2″ | .oo5-.008″ | .020″ | .025″ |
2-1/2” | .007-.010” | .021” | .030” |
3-1/2″ | .010-.012″ | .030” | .036″ |
4-1/2″ | .010-.013″ | .030” | .039″ |
6″ | .013-.016″ | .039” | .048″ |
8″ | .016-.019″ | .048” | .057” |
10″ | .018-.021″ | .054” | .063″ |
12″ | .020-.025” | .060” | .075″ |
Screws should be rebuilt when dimensions reach the worn clearance measurements as product quality is being affected. When dimensions reach the maximum clearance, performance (output and product quality) suffers greatly.
Here is a typical payback example using a 4.5” dia x 24:1 barrier screw processing polyolefin:
Nominal Rate – 1,500 lbs/hr
Melt Temperature – 420 to 430° F.
Output Stability – +/- 5%
Effects of diametrical wear factor of .025-.030 may result in a 60 lb/hr output reduction due to wear
Nominal Rate – 1,440 lbs/hr
Melt Temperature – 430 to 450° F.
Output Stability – +/- 10%
Penalty Cost: 60 lbs/hour x 0.65 = $ 65.00 /hour x 24 hours = $936.00 per day
A typical screw rebuild for a 4.5” Dia X 24:1 Barrier Screw with Colmonoy 56 hard surfacing costs $3,642. with a 2 week delivery.
Your Return on Investment Payback is 3.89 days
If you are planning on rebuilding your screws, take advantage of Xaloy’s screw rebuilding cell that features fast turnarounds (7– 14 days) on your screws. Streamlined using Lean manufacturing principals, we can receive incoming screws for inspection, estimate costs, quote and release to the shop with your approval within 24 hours of receiving the parts.
When to Repair an Extrusion Screw
As screws wear, the clearance between the screw flight and barrel wall increases, especially in the high pressure areas of the barrel. For example, a new 2.5” diameter screw will have 0.005” to 0.007” diameter clearance or approximately 0.003” on the radius.
When a 2.5” screw is worn to around 0.020” on the diameter clearance, a rate reduction will be noticed along with elevated melt temperature. It is common practice to speed up the screw to regain the output reduction. This results in even higher melt temperatures. Next, the barrel temperatures are lowered to overcome the higher melt temperature. At this point, the extruder is running at a higher rpm and lower barrel zone temperature settings than normal. The operator is not in control of the extrusion operation at this point. The worn screw is in control of your business. The extrusion operator is fighting a problem his company accepts, when he could be improving the bottom line by fine tuning the process to an inspect screw. The worn screw yields much more off spec extrusions than normal. This is money down the drain.
When a 2.5” screw is worn to around 0.030” on the diameter clearance, good quality product cannot be made and the efficiency of the operation is so low that money is being lost with every pound of product that is extruded. Regrind rates go up and finished product quality goes down. Operators are frustrated, QC is pressured to accept out of spec product, and the customer is complaining. At this point you are going out of business by letting your competitor in the door.
Note: The above recommendation is assuming the barrel is new or has no wear. As barrel wear would have to be added to the screw wear to get the total clearance.
You pay for screw repair whether you repair it or not. If you don’t know what your wear dimensions are, we have the tools and can measure your screws.
When to Replace an Extrusion Barrel
As barrels wear, the clearance between the screw flight and barrel wall increases, especially in the high pressure areas of the barrel. Buying a new screw for a worn barrel does not solve the clearance problem. It may make it better, but it is not a fix for a worn barrel. Since barrels only wear in the high pressure areas or where fusion of the polymer takes place, measuring the end of the barrel ID does not tell the whole story of wear. A bore gage should be used to measure wear all along the barrel. Keep in mind that the screw wear has to be taken into account with barrel wear to determine the total clearance. If you don’t know what your wear dimensions are, we have the tools and can measure your barrels.
Repairing Extrusion Barrels
In the injection molding markets, it is common to “re-sleeve” the high pressure end of the barrel. The last 20” or so of the barrel is re-sleeved. The screw is reciprocating back and forth.
Why don’t we recommend lining barrels in extrusion?
The barrels are longer. Example: 3.5” x 24:1 L/D is approximately 80” long, not including the feed throat. In extrusion (unlike injection molding) the screw only turns one direction. When several sleeves (sleeves 12-15” long) are heat shrunk in the barrel they do not match up evenly. To hone or grind out the inside diameter of the barrel would take hours and hours to perform, resulting in high cost. The hone will follow the highs and lows of the barrel and not yield a straight bore. All the time, the hone is wearing or reducing the thickness of the bimetallic liner that has been inserted.
Some customers in blown film applications have been led to believe they can get at least another 6 months to 1 year out of the barrel. WRONG!
Problems that may pop up later with barrel rebuilds:
- The sleeves can shrink and spin
- The sleeves can weld to the screw flights if too tight (caused by high and lows of honing barrel)
- They can have poor heat transfer from heater bands, due to different metals and space between OD of barrel tube and ID of new sleeves
All of the above is 60-75% of a new barrel cost. Do the right thing and purchase a new barrel!